Balancing Act: Can Petrochemicals Be Both Emissions Free and Zero-Waste?
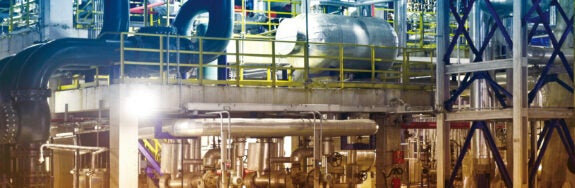
Even with the move to cleaner energy, the demand for fossil fuel feedstocks—think plastics and fertilizer—continues to grow. Here's why petrochemical producers should shoulder the embedded carbon burden.
At a Glance
Key Challenge
The petrochemical industry will represent a significant source of emissions and pollution long after the decarbonization of global energy systems.
Policy Insight
Regulating embedded emissions at the point of production could reduce the emissions as well as reduce petrochemical waste.
Executive Summary
As the global energy transition toward low carbon resources continues, our dependence on oil, natural gas, and coal as sources of fuel will diminish substantially. However, demand for these fossil resources will not disappear entirely. On the contrary, the world is experiencing, and will continue to experience, a rapid increase in demand for oil and natural gas as feedstocks for petrochemical products. This is perhaps most clearly seen in the planet’s demand for, and production of, plastics—almost all of which are derived from fossil fuels.
The production of petrochemicals is not immediately recognizable as a continuing source of carbon emissions, because much of the carbon from the fossil fuel feedstocks is trapped within the petrochemical products. However, as we now know, once disposed of, these highly stable plastic products contribute to perhaps the second greatest environmental catastrophe following climate change: the global plastic waste crisis. The defacto solution for this waste crisis is incineration, which then releases the carbon from plastics—making them no less emissions intensive that fossil derived fuels.
There are many possible strategies to be adopted that could reduce plastic waste production without creating another potent source of carbon emissions. However, promoting any of these technological solutions will require careful carbon accounting and skillfully-implemented policy solutions. This report attempts to illustrate why putting the burden of embedded carbon on the petrochemical producers may be essential to support a sustainable petrochemical industry.
As scientists, policy experts, and business leaders grapple with how best to transition to a sustainable economy, clean energy has rightly been identified as the single greatest opportunity to curb global carbon emissions. However, as the world works to achieve the emissions goals of the Paris Climate Agreement, it is important to recognize that decarbonizing our energy system alone will not lead us to a carbon-neutral (or negative) society.
With the exception of methane produced by livestock and land-use change, most carbon emissions being released today by humans can ultimately be traced back to the extraction of natural gas, coal, and oil (C2ES n.d.). These resources—the products of millions of years of naturally-sequestered organic material—will not cease to exist once we transition to an energy system entirely powered by zero-carbon energy sources. They will remain available for extraction and processing by the chemical industry.
In fact, many of the world’s largest oil and gas companies are already beginning to look ahead to a future in which the reserves they control will have lessened value as fuel, and are investing in processes that would increase the yield of high-value petrochemical feedstocks (Tullo 2019).
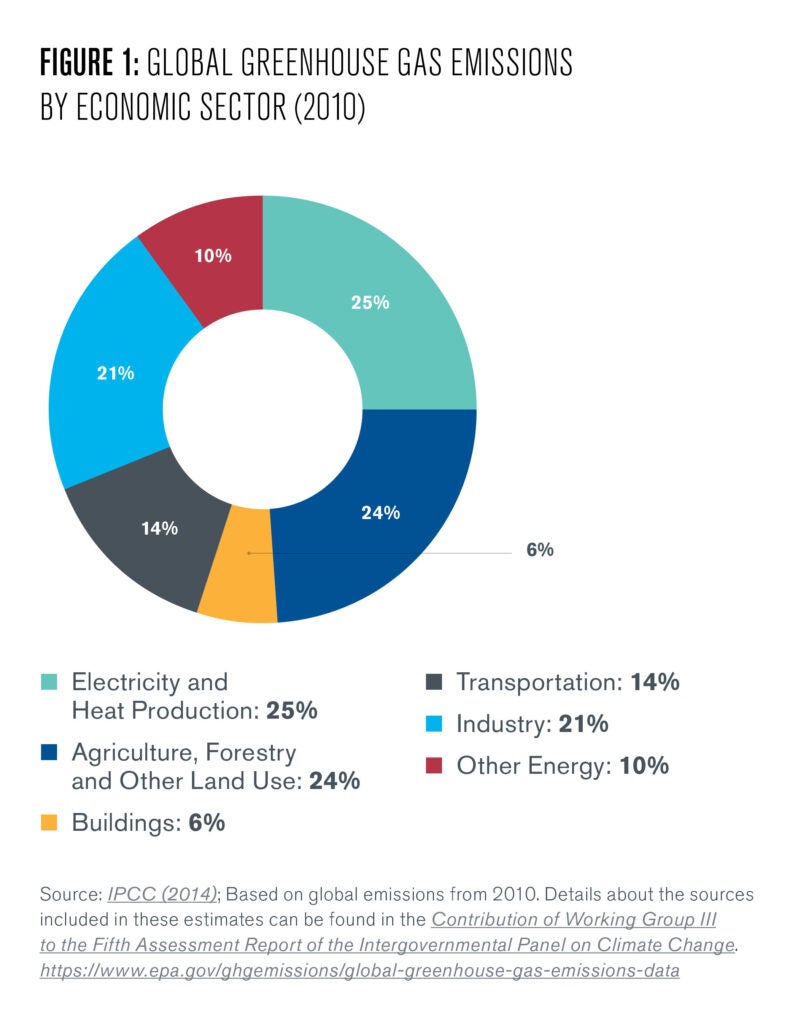
Currently, the industrial sector accounts for approximately a fifth of global greenhouse gas emissions, as calculated by its direct “process energy” demand, or the energy demanded to power industrial processes (See Figure 1). Most industries only require process energy; however, the petrochemicals industry demands both process energy and the energy embedded in the hydrocarbon feedstocks that are used to manufacture the petrochemical products.
This is why feedstock quantities are conventionally described in terms of joules rather than by volume, even though they are not used for energy generation. Crucially, the convention of assigning an energy value to feedstocks does not extend to the accounting of embedded carbon as portrayed in figure 1. Thus, even though chemicals is the most energy intensive industry, it is only the third most carbon intensive, after steel and cement (IPCC 2014). This is because as long as a petrochemical product exists, these carbon atoms are effectively sequestered.
In the United States between 1990 and 2016, for example, it is estimated that only 34 to 38% of potential carbon was released during the manufacturing of non-fuel petrochemical products (Environmental Protection Agency 2016), leaving more than 60% stored within the chemical products themselves.
However, this “storage” of carbon comes at a very significant price. Plastics are a major category of modern petrochemicals and the world already faces a plastic waste crisis that, after climate change, might be one of the most pressing ecological disasters of the 21st century (Woodring 2015). Today, there is a mass of plastic floating in the Pacific ocean that is approximately 15 times the size of the state of Pennsylvania (Snowden 2019). These petrochemical products take centuries to break down, and even then, microplastics can circulate through food chains with unknown long-term effects.
There is little chance of global plastic consumption decreasing, or even plateauing anytime soon. Advanced economies use up to 20 times as much plastic as developing countries, and plastic consumption is expected to accelerate in Africa and South Asia as local economies grow (International Energy Agency 2018). The majority of plastic waste (54-58%) is sent to landfills or contaminates ecosystems (OECD 2018), leading us towards the surreal midcentury scenario of potentially having more plastic in the oceans than fish (Kaplan 2016). The continued disposal of non-biodegradable petrochemical products simply cannot sustainably continue. For this reason, the concept of carbon “storage” within petrochemical products must also come to an end.
Rethinking Waste Management
If the world continues using petrochemical products at current or increased rates, it is critical that a strict end-of-life management plan for these products is developed which accurately accounts for embedded carbon. Incinerating petrochemical waste, for example, is an effective way of managing volume, but it also releases the carbon that was embedded in those products, mostly as CO2.
Currently, 24% of plastic waste is incinerated and is used to produce energy (EIA 2020). In our existing energy system, the energy produced through incineration is likely displacing emissions elsewhere in the energy system from oil, coal, or gas. This will not hold in a carbon-neutral energy system, and obscures the considerable quantity of carbon that is released through the incineration process (CIEL 2019). Ultimately, the incineration of plastic waste for energy is no more climate friendly than if the feedstocks used to produce that plastic had been burned directly.
As countries move to embrace renewable and other zero-carbon energy sources, oil and gas demand is poised to shift to the rapidly expanding petrochemical industry (Tullo 2019). As a result, a considerable share of our existing production of carbon dioxide will be diverted toward the production of plastics, fertilizers, and other chemical products unless alternative feedstocks are assimilated.
By supporting the production of alternative low-carbon and carbon-neutral feedstocks, we can ensure that the emissions reductions achieved by a transition away from oil, coal, and gas are maintained economy-wide. Before discussing these emerging solutions, it is critical to understand the feedstocks that these alternatives seek to replace.
What are Petrochemicals?
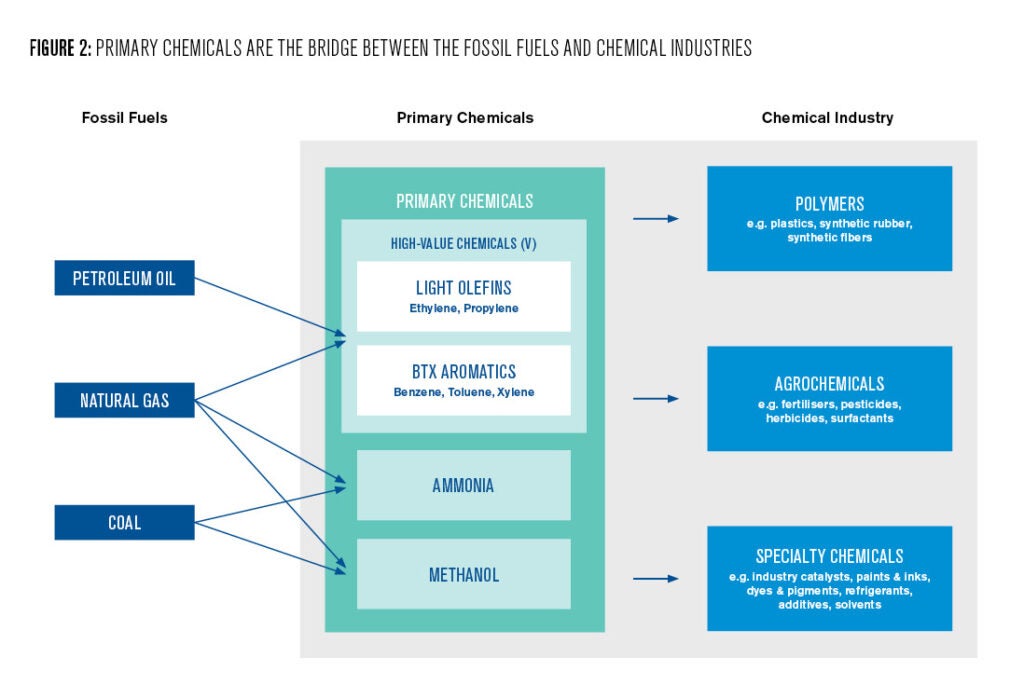
Petrochemicals are derived from petroleum oil, natural gas, and coal. While there exists a vast variety of petrochemicals, most are derived from only three sets of starting materials consisting of seven different molecules, collectively known as “primary chemicals” (IEA 2018). These chemicals are produced directly from fossil fuels and act as a gateway to the chemical industry.
Primary petrochemicals include the HVCs (high-value chemicals), methanol, and ammonia. These materials are used to produce most of the world’s plastic, synthetic textiles, and nitrogen fertilizers, along with over 100,000 specialty chemicals used in manufacturing, packaging, agriculture and beyond (IEA 2018).
HVCs include ethylene, propylene, and aromatic compounds collectively called BTX (benzene, toluene, and xylenes). These chemicals are predominantly produced as byproducts from refining petroleum oil, though ethylene and propylene can also be synthesized from natural gas. The choice of feedstock for HVCs depends on several factors including the production volume of the specific fossil fuel in the region (IEA 2018).
HVCs are used to make most of the world’s plastics and the end-of-life emissions are dependent on how these plastics are disposed of after use. In the case of incineration, most of the embedded carbon is released as CO2.
Methanol (CH3OH) is produced from a gaseous mixture composed of carbon monoxide (CO) and hydrogen (H2) called syngas. Syngas is traditionally produced from natural gas or coal. Similar to HVCs, the carbon atoms from these natural resources become embedded in methanol and its downstream products with varying end-of-life emissions.
For example, formaldehyde is one of the most important products of methanol and is used to produce thin film resins and adhesives. These products are typically embedded in other materials, making them difficult to recycle and are usually sent to landfills or incinerators at the end of their useful life thereby contributing to either the petrochemical waste crisis or climate crisis, respectively (Liu 2018).
Ammonia (NH3) is unique among this list of primary petrochemicals, because it does not contain any carbon. It is categorized as a petrochemical because the production relies on hydrogen gas derived from syngas. Rather than being embedded in the product itself, most of the carbon emissions associated with ammonia are released at the point of synthesis. More than half of globally produced ammonia is used to synthesize urea (CH₄N₂O), which is then used as fertilizer (IEA 2018).
Urea is produced by combining ammonia with a small percentage of the CO2 that is emitted during the production of ammonia. The incorporated CO2 is later released as gaseous emissions after the fertilizers decompose in the soil (Brown 2016). For this reason, a transition to using alternative carbon-neutral feedstocks would also eliminate the life-cycle carbon emissions of fertilizers.
A Growth in Supply and Demand
The global production of petrochemicals is poised for dramatic growth over the coming decades, due to expected increases in both demand and supply (Grand View Research 2020). In many developing countries, demand for fertilizer is increasing by 1 to 2% annually, and demand for plastic products is increasing even more rapidly; in places more than 10% annually (IEA 2018).
Only in the most well-developed nations has there been a plateau in annual demand for fertilizers at between 85 to 135 kg per capita. There are also some signs of a possible saturation of plastic in many of these nations at approximately 60 kg per capita per year. Fertilizers and plastics account for 70% (by mass) of overall petrochemical production.
If we assume a global cap of 100 kg of fertilizer per capita and 60 kg of plastic per capita for all nations, and maintain the 70% share of petrochemical production that these two categories currently hold, we can posit that the global capacity to consume petrochemicals is at least 1,784 million tonnes (Mt) per year—approximately twice current global production. If we also consider the likely possibility that continued innovation will let petrochemicals further displace other materials such as wood and metal, the global capacity for petrochemical consumption will be even higher (AFPM Communications 2019).
The fossil fuel industry is more than ready to meet this increasing demand. As noted previously, oil and gas producers are beginning to explore the possibility of increasing the petrochemical yield from refineries in an effort to hedge against an energy system in transition (Tullo 2017 and Chen 2019). As global demand for gasoline, diesel, and other fuel oils dissipates in the energy sector, oil producers want to find the best way to continue refining crude hydrocarbons into valuable products.
Today, approximately 12 million barrels per day (mb/d) of oil products, 105 billion cubic meters (bcm) of natural gas and 80 Mt of coal are used to produce new petrochemicals. An additional 190 Mt of natural gas liquids (NGL’s) and other refining byproducts are also used. Compared to the total global production of these resources, this represents roughly 14%, 10%, 1%, and 50% respectively (BP n.d., YCharts 2020, EIA 2020, IEA 2020, EIA International n.d.).
If global demand reaches the levels of today’s most developed countries, petrochemicals could use close to 30% of current annual oil production, 20% of global natural gas production, a relatively minor share of coal production, and nearly the entire current global supply of NGL’s. In this future, even if the global energy system transitions entirely away from fossil fuels, a considerable portion of the world production of fossil fuels will continue to enter our economy in the form of petrochemicals, all with the potential to eventually release their embedded carbon during end-of-life processing.
Alternative Feedstocks
Recycling
The most commonly used alternative feedstock for petrochemicals—though perhaps not always thought of in this way—is other petrochemical waste. Recycling of plastics and synthetic fibers is already a relatively common practice around the world, but several interrelated factors make large-scale recycling of petrochemical waste an ongoing challenge. In an ideal world, there would be no need to consider or account for the embedded carbon in plastics and other non-fertilizer chemicals, because they would all be recycled back into new products.
Unfortunately, only about 18% of global annual plastic waste is currently being reprocessed into new plastic products (IEA 2018). Some plastics, called thermosets, are inherently non-recyclable, due to their inability to be melted or reformed. However, the majority of plastics, called thermoplastics, can theoretically be recycled. This means that how to effectively recycle plastics is as much a question of logistics and economics as it is a question of chemistry.
Only about 20% of plastic waste is ever collected for recycling and there are significant costs associated with transporting and consolidating globally dispersed waste (IEA 2018). Furthermore, traditional recycling methods also result in a significant portion of plastics being “down-cycled” into lower-grade products due to impurities. The logistics of global recycling was recently further complicated by China’s decision to no longer accept many shipments of plastic waste for fear of the environmental and social burden it places on local ecosystems and people (Nargi 2019).
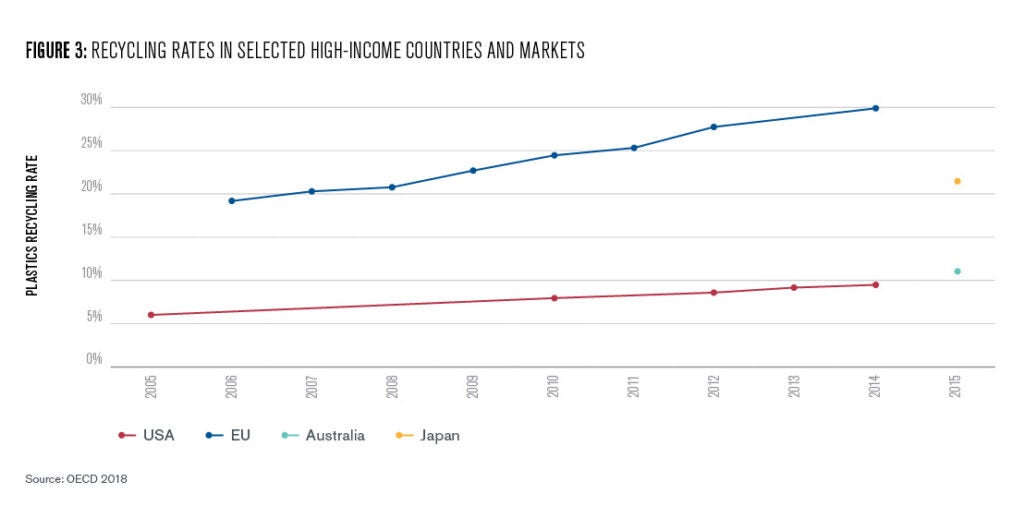
While current global recycling rates for plastics are low, there is significant opportunity for improvement, as demonstrated by a number of individual countries. Taiwan, for example, has implemented an aggressive waste management system for decades, which has led to recycling more than 50% of its municipal waste (Simon 2019). Their 4-in-1 Recycling Program (EPA Taiwan 2020) puts the onus to recycle on both consumers and the private sector, and by doing so, has helped Taiwan build a multi-billion-dollar recycling industry (Bush 2019).
The European Union also has an ambitious plastics strategy (Network for Circular Plastics Packaging, 2019) that sets the goal of either reusing or recycling all plastic packaging by 2030. Although today, only about 30% of overall waste is processed into new products (Figure 3, OECD 2018).
In order for countries to achieve much higher recycling rates, multiple forms of recycling need to be considered and ardently supported. There has recently been growing interest in manufacturing plastics designed for reuse, for example: packaging, manufacturing, and consumer goods. Reuse of petrochemical products not only avoids waste and the need to produce new products, it also has the potential to be very cost-effective, especially for the consumer (Network for Circular Plastics Packaging 2019).
Petrochemical waste is an invaluable source of carbon neutral feedstocks, addressing both waste and emissions simultaneously. However, technical and logistical challenges mean that even with extremely ambitious and rigorous national recycling initiatives, countries have struggled to successfully recycle even a majority of petrochemical waste (See Figure 3). As the rate of chemical consumption increases, traditional recycling methods alone are unlikely to sufficiently reduce the rate of petrochemical pollution, meaning that incineration will likely continue to be a needed method of waste management.
Alternative ways of producing carbon neutral feedstocks, beyond product recycling, must be utilized for the global petrochemical industry to meet the projected growth in demand without increasing embedded carbon emissions. Fortunately, thanks to the relative simplicity of the seven primary petrochemicals, many non-fossil fuel feedstocks could be utilized. Although the following processes are all technologically feasible, they will all require continued innovation and market support in order to meet global demand.
Renewable Syngas
Production of renewable syngas could decrease emissions from methanol and its derived products. One existing process employs biomethane (methane captured during anaerobic digestion of biomass or biological waste) to produce syngas using technologies similar to traditional methods for processing methane derived from natural gas.
Alternatively, the carbon monoxide and hydrogen gas can be obtained from the respective electrolysis of CO2 and water (Smith 2019). If the electrolysis is powered by carbon-neutral electricity, then the afforded syngas is, effectively, renewable. As more contries and companies invest in hydrogen infrastructure, the economics of this process stands to improve dramatically (Patel 2020).
Biologically Derived Chemical Building Blocks
Biological feedstocks are considered a renewable resource because all of the CO2 contained within these materials is sequestered from the atmosphere during the lifetime of the source plant. This distinguishes them from fossil fuels, which contain sequestered CO2 from millions of years in the past.
Biologically derived molecules are structurally different and much more varied than the molecules in fossil fuels. Therefore, in order to improve the efficiency of producing chemical feedstocks from biological material, it is essential that new methods for utilizing this wide array of molecules are developed.
The generation of renewable syngas using biomethane is one simple example of deriving chemicals from biological sources, but synthesis of more complex molecules is also possible. Ethylene (C2H4) is the starting material for polyethylene, a prominent ingredient in the manufacturing of a wide range of plastics. While traditional synthetic routes use natural gas or naphtha (a product of oil distillation) in a process known as cracking, biologically derived ethylene can be produced by dehydrating ethanol (C2H6O) (Mohsenzadeh 2017).
Ethanol, already the bedrock of the bioenergy industry, can be produced from sugars and starches found in a wide range of already harvested crops. In Brazil, a company called Braskem is already commercially producing chemicals-grade ethylene and polyethylene from sugarcane (Braskem n.d.).
Production of chemical feedstocks could offer the emerging bioenergy industry an alternative revenue stream and, depending on the region, could perhaps be competitive with other methods of local ethylene and methanol production. This is unlikely to be true in the United States because of the country’s plentiful and low-cost natural gas resources. In countries without easily accessible or affordable natural gas reserves, however, biomethanol and bioethylene production could be a viable business model.
Renewable Hydrogen for Ammonia Production
The molecular building blocks needed for the production of ammonia are nitrogen (N2) and hydrogen (H2) gas. Given its abundance in air (80% of our atmosphere), nitrogen gas is considered a renewable resource. By supplying pure H2 from renewably powered electrolysis, one could not only decarbonize the process of ammonia production but could also reasonably remove it from consideration as a petrochemical.
In a previous Kleinman Center report, we discuss how production of hydrogen from water using electrolysis is still extremely energy intensive and, as a result, fairly expensive (Serpell et al. 2019). This high cost is a significant barrier to utilizing renewable hydrogen at an industrial scale. Fortunately, many in the energy sector are motivated to increase the efficiency of the water electrolysis reaction and lower production costs.
Advances in this area will unlock the enormous potential of hydrogen as a source of stored energy and distributed thermal energy in a clean energy future (Deign 2019). Producing sufficient hydrogen to offset the fossil fuel demands of ammonia production would alone have a considerable effect on the future carbon intensity of the fossil fuel industry.
Chemical Recycling (Depolymerization)
Chemical recycling is the concept of breaking down waste products into their original molecular building blocks using chemical reactions. While traditional mechanical recycling remolds or reshapes the same polymers into new uses (complete with structural weaknesses and impurities), depolymerization allows products to be repurposed into entirely new materials that utilize the same building blocks and removes any of the purity concerns inherent in mechanical recycling methods. In other words, this is the truest form of recycling as a source of alternative feedstocks.
Although depolymerization technologies are not currently applicable on a commercial scale and significant research and investment is still needed, chemical recycling can, in theory, allow for higher efficiencies than traditional mechanical recycling methods (Thiounn and Smith 2020). Successful development of large-scale chemical recycling could particularly impact the lifetime emissions of plastics that are traditionally thought of as non-recyclable (e.g. thermoset plastics and plastics with stringent purity requirements such as food grade plastics) but will require future innovations in waste stream separation and purification as well as the development of more effective catalysts needed to reduce operating temperatures.
Policy Solutions
In order to reduce the eventual end-of-life carbon emissions of petrochemicals, it is necessary to “price-in” the cost of those emissions somewhere along the value chain. One solution would be to place this additional cost on the incinerator—in other words, the direct polluter who is using petrochemical waste to generate energy and in doing so, is releasing the embedded carbon. The alternative solution would be to assign the social cost of carbon to the producers who are responsible for embedding the carbon from fossil fuels in the first place.
If carbon emissions were the only externality that demanded consideration in the production and processing of petrochemicals, then it should not matter whether these externalities are priced in at the beginning or the end of the life-cycle. Either way, these costs will disperse through the market by increasing initial product costs or by increasing end of life processing costs.
However, in the case of petrochemicals, climate change is not the only relevant externality. Petrochemcials themselves, specifically plastics, carry a considerable externalized cost depending on the end-of-life processing method that is used. Taxing carbon at the direct source (incinerators) would decrease the competitiveness of incineration as a waste solution, but would shift post-consumer processing of plastics to landfills and recycling. Taxing incinerators may reduce carbon emissions from the petrochemical industry, but in doing so could actually add to the plastic waste crisis by handicapping an effective method of plastic reduction.
Instead, by charging the producers for carbon based on the full amount of embedded carbon, you effectively capture a larger percentage of the potential emissions from petrochemicals and by doing so simultaneously drive the industry away from incineration and landfills and toward recycling. Carbon taxation at the point of production could also be coupled with incentives for companies to take a more active role in the life-cycle processing of their products and to use recycled feedstocks in their products.
These policies could also be used to track the quantity of renewable and non-renewable carbon entering the industry and allow commercial consumers of raw petrochemicals to knowingly opt for suppliers that use carbon-neutral or low-carbon feedstocks. This imposition of a carbon price on producers could be coupled with additional fees for landfill disposal, which would further reduce the quantity of petrochemical waste that goes unprocessed.
Following Taiwan’s model, partnerships between industry, government, and consumers could result in significantly improved plastics management systems to tackle logistical hurdles. There, manufacturers and importers are responsible for paying a fee to Taiwan’s Environmental Protection Administration, which contributes to some of the costs associated with collecting and recycling those products at the end of their useful life (Rapid Transition Alliance 2019). Additionally, consumers are required to purchase specific bags for different types of waste disposal, each priced according to the type of waste, as a way to further offset the costs of recycling.
Making products that can be cheaply and easily repurposed is only half of the challenge. Collection, sorting, and public buy-in is equally, if not more, important in order to dramatically increase the rate of recycling of petrochemical waste.
Products that have longer lifetimes and can be reused can minimize the need for additional plastic to be created. This will result in a lower end-of-life emissions per use, and will reduce the cost to manufacturers of using recycled feedstocks. Other countries, including the U.S., could adopt similar policies to support consumer and producer-driven solutions, although the specifics of policy design and implementation will greatly depend on the country’s system of governance and available infrastructure.
These policies, in combination, could address both the high level of non-renewable carbon entering the petrochemical production stream, as well as the low rate of post-consumer processing of petrochemical waste.
Conclusion
The ultimate goals of a sustainable petrochemical industry are clear. On the one hand, solutions must be found for the current petrochemical waste crisis, especially plastic waste. Failure to introduce new systems, and extend existing systems, for post-consumer management and processing of an ever-expanding volume of petrochemical goods will lead to a global ecological and economic crisis, perhaps second only to the climate crisis. Both crises are symptoms of an economic system that does not adequately internalize the global costs of pollution.
Unfortunately, one of the most common methods of managing post-consumer petrochemical waste is to incinerate it—reducing the volume of disposed and non-biodegradable waste, but at the same time releasing the carbon contained within that waste. Recycling offers an alternative solution to the waste crisis, but struggles to compete economically with virgin chemical feedstocks derived from fossil fuels. Therefore, the second goal of a sustainable petrochemical industry must be to reduce dependence on fossil fuels for feedstocks and instead invest in carbon-neutral alternatives.
If business as usual production and end-of-life processing of petrochemicals is allowed to continue, it will have significant and highly detrimental impacts on our ability to fight both the climate and plastic waste crises. As the oil and gas industry looks for new sources of demand for fossil fuel in a future of renewable energy, there will be even greater pressure on the petrochemical industry to continue relying upon unsustainable and carbon intensive fossil fuel derived feedstocks. This will in turn reduce the competitiveness of recycled products and could, without intervention, lead to an even greater rate of plastic disposal and incineration.
The best way to prevent this trend within the petrochemical industry is to institute a broad set of pollution-focused fees and regulations at several points along the life-cycle of petrochemicals. By implementing these policies, the world can continue deploying highly useful petrochemical products in ways that are not only environmentally benign, but could also significantly help decarbonize our society by allowing for the production of cheaper and lighter vehicles, solar panels, and a wide range of other consumer products. Petrochemicals can also continue to increase productivity of agricultural land, thereby reducing the global need for deforestation and other ecosystem disruption.
AFPM Communications. 2019. “Renewable Energies Rely on Petrochemicals from Oil and Natural Gas.” Accessed 12/21/20: https://www.afpm.org/newsroom/blog/renewable-energies-rely-petrochemicals-oil-and-natural-gas#:~:text=Solar%20energy%20is%20not%20alone,engine%20houses%20and%20rotor%20blades.
Aizhu, Chen. 2019. “China’s Zhejiang Petrochemical Launches Mega Reformer Unit.” Reuters, Singapore. Accessed 12/21/20: https://www.reuters.com/article/china-petrochemical-zhejiang/chinas-zhejiang-petrochemical-launches-mega-reformer-unit-idUSL4N28L0PU
BP n.d. “Statistical Review of World Energy: Approximate Conversion Factors.” Accessed 12/21/20: https://www.bp.com/content/dam/bp/business-sites/en/global/corporate/pdfs/energy-economics/statistical-review/bp-stats-review-2019-approximate-conversion-factors.pdf
Braskem, n.d. “Profile.” Accessed 12/21/20: https://www.braskem.com.br/profile
Brown, Trevor. 2016. “Urea Production is Not Carbon Sequestration.” Ammonia Industry. Accessed: 12/21/20: https://ammoniaindustry.com/urea-production-is-not-carbon-sequestration/#:~:text=To%20make%20urea%2C%20fertilizer%20producers,through%20the%20production%20of%20urea.
Bush, Jessica. 2019. “Taiwan Has Found A Brilliant Way to Get More People to Recycle.” Buzzworthy.com. Accessed 12/21/20: https://www.buzzworthy.com/taiwan-garbage-disposal/
Center for Climate and Energy Solutions. n.d. “Global Emissions.” Accessed 12/21/20: https://www.c2es.org/content/international-emissions
Center for International Environmental Law. 2019. “Plastic & Climate: The Hidden Costs of a Plastic Planet.” Washington D.C., USA. Accessed 12/21/20: https://www.ciel.org/plasticandclimate/
Deign, Jason. 2019. “10 Countries Moving Toward a Green Hydrogen Economy.” Accessed 12/21/20: https://www.greentechmedia.com/articles/read/10-countries-moving-towards-a-green-hydrogen-economy
Environmental Protection Agency. n.d. “Global Greenhouse Gas Emissions Data.” Washington D.C., USA. Accessed 12/21/20: https://www.epa.gov/ghgemissions/global-greenhouse-gas-emissions-data
Environmental Protection Agency, 2016. “Inventory of U.S. Greenhouse Gas Emissions and Sinks: 1990 – 2014.” Washington D.C., USA. Accessed 12/21/20: https://www.epa.gov/ghgemissions/inventory-us-greenhouse-gas-emissions-and-sinks-1990-2014
Environmental Protection Administration (Taiwan). 2020. “The 4-in-1 Recycling Program.” Taipei City, Taiwan. Accessed 12/21/20: https://recycle.epa.gov.tw/en/recycling_knowledge_01.html
Grand View Research. 2020. “Plastic Market Size, Share & Trends Analysis Report by Product (PE, PP, PU, PVC, PET, Polystyrene, ABS, PBT, PPO, Epoxy Polymers, LCP, PC, Polyamide), By Application, By Region, And Segment Forecasts, 2020 – 2027.” Accessed 12/21/20: https://www.grandviewresearch.com/industry-analysis/global-plastics-market
International Energy Agency. 2020. “Coal Information: Overview.” Accessed 12/21/20: https://www.iea.org/reports/coal-information-overview
International Energy Agency. 2018. “The Future of Petrochemicals.” Accessed 12/21/20: https://www.iea.org/reports/the-future-of-petrochemicals
Fischedick M., J. Roy, A. Abdel-Aziz, A. Acquaye, J. M. Allwood, J.-P. Ceron, Y. Geng, H. Kheshgi, A. Lanza, D. Perczyk, L. Price, E. Santalla, C. Sheinbaum, and K. Tanaka. 2014. “Industry” In: Climate Change 2014: Mitigation of Climate Change. Contribution of Working Group III to the Fifth Assessment Report of the Intergovernmental Panel on Climate Change. Cambridge University Press, Cambridge, United Kingdom and New York, NY, USA. Accessed 12/22/20: https://www.ipcc.ch/site/assets/uploads/2018/02/ipcc_wg3_ar5_chapter10.pdf
Kaplan, Sarah. 2016. “By 2050, There Will Be More Plastic than Fish in the World’s Oceans, Study Says.” The Washington Post. Accessed 12/21/20: https://www.washingtonpost.com/news/morning-mix/wp/2016/01/20/by-2050-there-will-be-more-plastic-than-fish-in-the-worlds-oceans-study-says/
Liu, M., Wang, Y., Wu, Y. and Wan, H. 2018. “Hydrolysis and Recycling of Urea Formaldehyde Resin Residues.” Journal of Hazardous Materials, 355: 96-103. Accessed 12/21/20: https://pubmed.ncbi.nlm.nih.gov/29775883/
Mohsenzadeh, A., Zamani, A. and Taherzadeh, M.J. 2017. “Bioethylene Production from Ethanol: A Review and Techno‐economical Evaluation.” ChemBioEng Reviews, 4: 75-91. doi:10.1002/cben.201600025
Nargi, Lela. 2019. “We Can’t Send Plastic to China Anymore. What Happens to our Recyclables Now?” Washington Post. Accessed 12/21/20: https://www.washingtonpost.com/lifestyle/kidspost/we-cant-send-plastic-to-china-anymore-what-happens-to-our-recyclables-now/2019/11/25/ce76d020-065a-11ea-8292-c46ee8cb3dce_story.html
Network for Circular Plastics Packaging, Danish Plastics Foundation. 2019. “Design Guide-Reuse and Recycling of Plastic Packaging for Private Consumers.” Accessed 12/21/20: https://plast.dk/wp-content/uploads/2019/12/Design-Guide-Reuse-and-recycling-of-plastic-packaging-for-private-consumers-english-version-1.pdf
OECD 2018. “Improving Marets for Recylced Plastics: Trends. Prospects and Policy Responses.” OECD Publishing, Paris. Accessed 12/21/20: https://www.washingtonpost.com/news/morning-mix/wp/2016/01/20/by-2050-there-will-be-more-plastic-than-fish-in-the-worlds-oceans-study-says/
Organisation for Economic Cooperation and Development (OECD). 2018. “Improving Plastics Management: Trends, Policy Responses, and the Role of International Co-operation and Trade.” OECD publishing, Paris. Accessed 12/21/20: https://www.oecd.org/environment/waste/policy-highlights-improving-plastics-management.pdf
Patel, 2020. “Is Hydrogen the Power Industries Holy Grail?” Power Magazine. Accessed 12/21/20: https://www.powermag.com/is-hydrogen-the-power-industrys-holy-grail/
Rapid Transition Alliance. 2019. “Taiwan’s Transition – from Garbage Island to Recycling Leader.” Accessed 12/21/20: https://www.rapidtransition.org/stories/taiwans-transition-from-garbage-island-to-recycling-leader/
Simon, Stefan. 2019. “Taipei Trash and Recycling: A Quick and Easy Guide.” The New Lens. Accessed 12/21/20: https://international.thenewslens.com/article/117330
Smith, Wilson A. 2019. “Pathways to Industrial-Scale Fuel out of Thin Air from CO2 Electrolysis.” Joule. Accessed 12/21/20: https://www.sciencedirect.com/science/article/pii/S2542435119303538
Snowden, Scott. 2019. “300-Mile Swim Through the Great Pacific Garbage Patch Will Collect Data on Plastic Pollution.” Forbes. Accessed 12/21/20: https://www.forbes.com/sites/scottsnowden/2019/05/30/300-mile-swim-through-the-great-pacific-garbage-patch-will-collect-data-on-plastic-pollution/?sh=46ae58e489fe
Thiounn, Timmy and Smith Rhett, 2020. “Advances and Approaches for Chemical Recycling of Plastic Waste.” Journal of Polymer Science. Accessed 12/21/20: https://onlinelibrary.wiley.com/doi/full/10.1002/pol.20190261
Tullo, Alexander. 2019. “Why the Future of Oil Is in Chemicals, Not Fuels.” Chemical & Engineering News. Accessed 12/21/20: https://cen.acs.org/business/petrochemicals/future-oil-chemicals-fuels/97/i8
Tullo, Alexander. 2017. “Aramco and SABIC Advance Oil-to-Chemicals.” Chemical & Engineering News. Accessed 12/21/20: https://cen.acs.org/articles/95/i48/Aramco-SABIC-advance-oilchemicals.html
U.S. Energy Information Administration. 2020. “Short-term Energy Outlook: Natural Gas.” Accessed 12/21/20: https://www.eia.gov/outlooks/steo/report/natgas.php
U.S. Energy Information Administration. “Biomass Explained: Waste to Energy.” Accessed 12/21/20: https://www.eia.gov/energyexplained/biomass/waste-to-energy.php
Woodring, Douglas. 2015. “Plastic Waste More Pressing Than Climate Change.” Wharton Magazine. Accessed 12/21/20: https://magazine.wharton.upenn.edu/digital/is-plastic-waste-more-pressing-than-climate-change/
YCharts. 2020. “World Crude Oil Production.” Accessed 12/21/20: https://ycharts.com/indicators/world_crude_oil_production
Oscar Serpell
Deputy DirectorOscar Serpell oversees all student programming, alumni engagement, faculty and student grants, and visiting scholars. He is also a researcher, writer, and policy analyst working on research initiatives with students and Center partners.
Wan-Yi “Amy” Chu
Assistant Professor, Mills College, Oakland, CaliforniaWan-Yi “Amy” Chu is an assistant professor in Chemistry at Mills College in Oakland CA and a former postdoctoral researcher for the Goldberg Group at the University of Pennsylvania.
Benjamin Paren
Alumni Research FellowBenjamin Paren is an alumni research fellow at the Kleinman Center and a postdoctoral research associate in the Research Laboratory of Electronics at the Massachusetts Institute of Technology.