
Critical Mineral Recovery in Industrial Waste
The massive waste produced by industries over the last century is more than just a burden on the environment—it’s an opportunity. By repurposing materials like mining waste and coal ash, we can source critical minerals essential for clean energy and safely store carbon, reducing hazards while boosting U.S. energy security.
For more than a century, industry has discarded massive amounts of waste products that contribute significantly to the environmental footprints of industries and pose hazards to communities and ecosystems. These abundant materials hold untapped potential for critical mineral sourcing and carbon storage, both of which are vital for supporting the energy transition.
Materials that were once discarded—and are currently environmental hazards—can be transformed into valuable resources by identifying their value. Examples of such waste streams include fly ash from coal combustion, mining waste, municipal solid waste, and phosphogypsum waste from fertilizer production.
These materials are rich in minerals essential for the clean energy industries. Referred to as the “dynamic dozen,” they include graphite, nickel, lithium, neodymium, dysprosium, praseodymium, cobalt, manganese, iridium, platinum, gallium, and germanium. The U.S. Department of Energy (DOE) has released a funding notice for the large-scale exploration and development of sourcing rare earth elements and critical minerals (REEs and CMs) from unconventional industrial byproducts.
Domestic production of CMs is key to enhancing energy security by reducing dependence on international supply chains. The U.S. currently imports over 80% of the national critical mineral supply. By developing a domestic supply and demand system, we can contribute to overall energy security while mitigating the environmental and health hazards posed by legacy stockpiled industrial waste.
Recovering these minerals involves innovative separation techniques. Physical methods sort particles by size, density, or magnetism, often minimizing the need for harsher chemical processes. Chemical separation methods are used when necessary, though they are more energy-intensive. These methods not only enable mineral recovery but can also transform waste for climate solutions, like mineral carbonation.
At the University of Pennsylvania’s Clean Energy Conversions Lab, Professor Jennifer Wilcox’s team uses physical and chemical processes to enrich minerals from waste, creating valuable feedstocks for carbon storage. Yet, addressing environmental impacts and sourcing sustainably requires a broader, standardized approach. The International Organization for Standardization (ISO) helps set guidelines to ensure responsible practices, though the current standards often react to established methods instead of pioneering new ones. While ISO standards focus on environmental and social sustainability, representation from marginalized groups remains limited.
Communities affected by hazardous waste could see improved health as these materials are safely processed and recycled. This approach may also revitalize regions around waste sites, creating jobs and attracting investment. The DOE’s CORE-CM initiative highlights this potential by supporting projects that both recover valuable minerals and serve community needs. Such efforts can strengthen the U.S. critical mineral supply chain while providing local economic benefits.
The University Training and Research (UTR) Program also plays a role in this transition, focusing on workforce development through two subprograms: one for Historically Black Colleges and Universities and other Minority-Serving Institutions (HBCU-MSI) and another focused on carbon research. These programs aim to train the next generation of engineers and scientists, equipping leaders from historically impacted communities with technical and economic skills crucial for the energy transition. For example, a new mining engineering program at Tennessee State University addresses workforce needs and a new program which combines STEM with humanities skills teaches students to foster public outreach and community leadership in sustainable energy solutions.
These initiatives—securing domestic minerals, responsibly storing CO2, and training skilled professionals—demonstrate a coordinated approach toward energy transition. Through a blend of incentives and public resources, the U.S. aims to build resilience, equity, and sustainability for future generations.
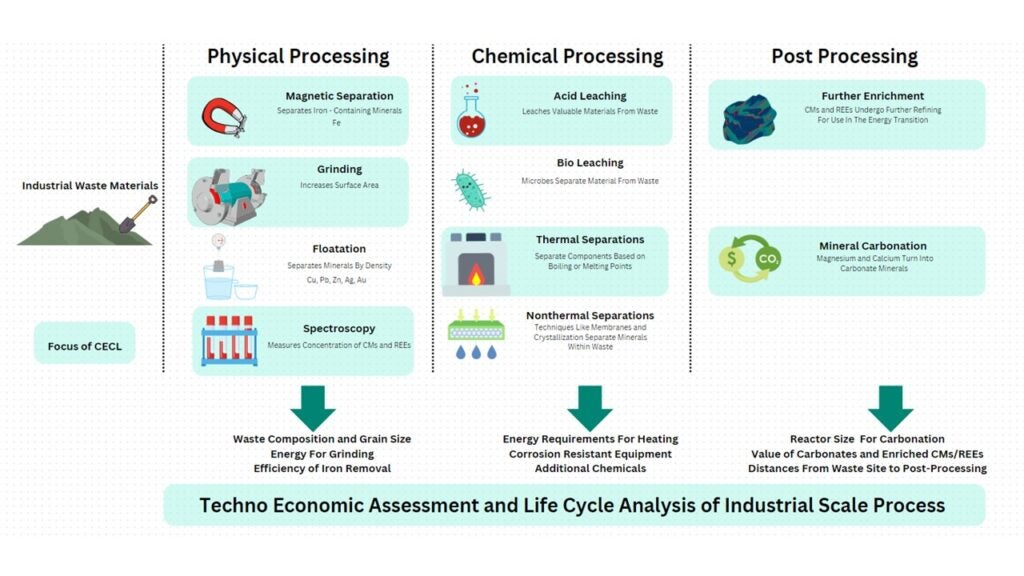
Katherine Vaz Gomes
Student Advisory Council MemberKatherine Vaz Gomes recently defended her Ph.D. in chemical engineering at the University of Pennsylvania. She is a graduate research assistant in the Clean Energy Conversions Lab and a member of the Kleinman Center’s Student Advisory Council.
Shelvey Swett
PhD Candidate , Chemical and Biomolecular EngineeringShelvey Swett is a third year PhD candidate in the Chemical and Biomolecular Engineering department at the University of Pennsylvania. Her work focuses on carbon capture and storage and on the recovery of critical minerals.
Jennifer Wilcox
Presidential Distinguished ProfessorJen Wilcox is Presidential Distinguished Professor of Chemical Engineering and Energy Policy. Her research expertise is in carbon capture and sequestration technologies, in order to minimize the negative impacts of fossil fuels.