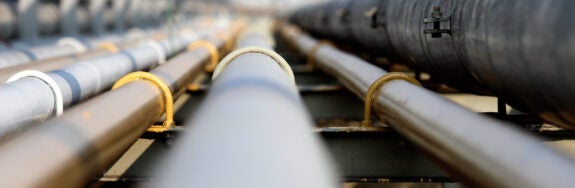
Compressed or liquefied hydrogen has many attractive properties as a store of carbon-free energy, such as its relatively high energy density and chemical stability. However, many experts suggest that using ammonia as a temporary vector for hydrogen will be needed to overcome the storage and transportation challenges associated with hydrogen. This digest looks at the round-trip energy efficiency of storing and transporting pure hydrogen vs ammonia.
At A Glance
Key Challenge
Hydrogen can offer carbon free energy storage, but containing and transporting presents considerable engineering challenges.
Policy Insight
The best strategy for storing and transporting hydrogen depends largely on the expected duration of storage and distance of transportation. For short duration storage, the energy demand of ammonia synthesis and cracking far exceed gas in storage efficiency.
Introduction
The use of hydrogen as a zero-carbon fuel for transportation, energy storage, and difficult-to-decarbonize industries is a very attractive idea for policy makers and industry alike. After all, hydrogen is lightweight, stable, and energy dense (when compressed or liquefied). These qualities replicate many of the distinct advantages of fossil fuels, but without directly emitting carbon dioxide or other planet-warming compounds.
However, the practical storage and transportation of hydrogen poses significant challenges, for which several studies (Royal Society 2020) have suggested the use of ammonia as a possible solution. Ammonia is already used extensively in agriculture, is distributed throughout much of the United States via an established network of pipelines and can be liquefied at relatively low pressures and high temperatures.
Compared to hydrogen and fossil fuels, it also poses little risk of combustion. As demand for hydrogen within the energy system grows, storage of hydrogen in the form of ammonia could mitigate many of the practical challenges to hydrogen utilization as a renewable fuel. However, this solution assumes a carbon-neutral method for synthesizing (creating) and cracking (breaking into constituent parts) ammonia, processes that today remain costly and energy intensive.
This digest explores how the incorporation of ammonia as a storage medium would impact the roundtrip energy efficiency of a carbon-neutral hydrogen network. We offer insights into the conditions that must be met for ammonia storage to be technologically feasible and economically preferable over compressed or liquefied hydrogen storage. Finally, we explore the infrastructure considerations for each fuel, independent of its roundtrip energy efficiency.
Hydrogen’s Role in the Energy Transition
The transition of our energy system to primarily intermittent and variable energy sources such as wind and solar will introduce wide-reaching energy storage challenges. The ability to easily store and transport the energy contained within fossil fuels has been the primary reason for their primacy since the early industrial revolution and continues to be a significant factor in our slow retreat from them.
By transitioning away from carbon-based energy sources, we are creating an energy storage vacuum that must be filled by new, emissions-free technologies. Two promising emissions-free technologies for filing this void are electrochemical batteries and hydrogen storage.
Electrochemical batteries such as the lithium-ion cells have improved rapidly over recent years in terms of efficiency, safety, energy and power density, and cost. Functionally, they are well suited for applications where the cells are cycled relatively frequently. However, even the most ambitious and optimistic development roadmaps for battery density, cost, and longevity fall short of fulfilling the long-duration, grid-scale storage demands of a decarbonized future (Mauler et al. 2021).
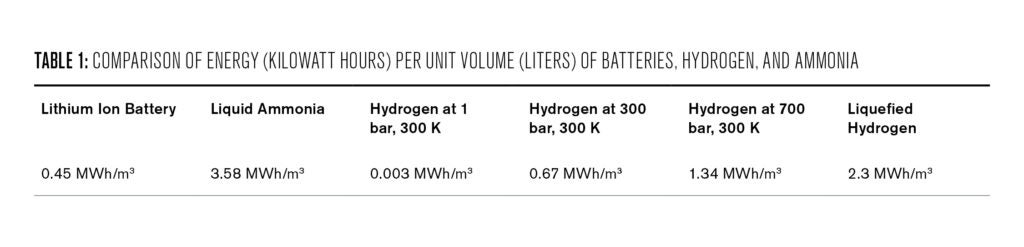
Existing lithium-ion cells can be permanently damaged if left uncharged and will slowly lose charge over time, limiting their usefulness for long-duration storage cycles. Electrochemical batteries are also heavy and have relatively low energy density (>0.5 kWh/L), making many applications such as in long-distance commercial air travel completely impractical.
Hydrogen could serve as exactly the complementary storage solution that we need for deep decarbonization. Renewable electrolysis allows hydrogen to effectively serve as a stable store of energy which can then be converted back to electricity using hydrogen fuel cells or thermal energy through combustion.
Unlike batteries, which need to be transported by road or rail, hydrogen could, in theory, be moved long distances through pipelines or compressed as a lightweight fuel alternative for air travel. Because it does not degrade from disuse, hydrogen could be a favorable alternative to lithium-ion cells in long-duration storage applications.
How Hydrogen Is Made
The majority of hydrogen produced today is made using a process called steam methane reforming (SMR). This process uses methane as a feedstock and produces CO2 as a byproduct. If hydrogen is going to play a role in a carbon-neutral energy future, carbon-neutral methods for producing it will need to be deployed at scale.
Currently, a rainbow of color-coded hydrogen production methods exist that could supplant SMR as the dominant method of production in a clean energy future. Each of these alternative methods seeks to prevent the production of carbon emissions by leveraging either carbon capture and sequestration (CCS) or carbon-neutral electricity or heat.
Electrolysis, the splitting of water into hydrogen and oxygen, is one of the most promising methods of producing hydrogen without the use of fossil fuels and will be the assumed production method for this digest. The analysis could easily be replicated assuming an alternative method of carbon-neutral hydrogen production.
The Limitations of Hydrogen
Unlike fossil fuels, which are extracted as an energy-producing natural resource, hydrogen must be synthesized. This is because it occurs naturally in low atmospheric concentrations and capturing hydrogen is not economically viable for the scale required in the energy sector. Instead, it is produced by breaking down other molecules like methane or water using industrial processes.
Therefore, hydrogen cannot serve as a net source of renewable energy—its only utility is in its ability to store energy. Hydrogen stores 33.6 megawatt hours (MWh) of energy per ton of hydrogen. However, the current best available technology to produce hydrogen electrolytically requires approximately 48 MWh per ton of hydrogen. This difference between the amount stored and the amount required to drive electrolysis is considered an inefficiency.
Additional energy is also required to convert hydrogen back into usable energy. This process can be achieved through a fuel cell or an internal combustion engine (ICE). Hydrogen fuel cells can derive a theoretical maximum energy output of 33.6 kWh/kg of hydrogen; however, most only achieve efficiencies of about 60%.
Energy yield from hydrogen combustion is similarly limited by the same maximum energy output (approximately 33.33 kWh/kg). Whereas traditional ICEs can scrape past 50% efficiency, hydrogen ICEs achieve about half that efficiency making them largely impractical as a clean transportation solution.
Since they are converting heat energy into kinetic energy, these efficiencies, combined with the energy requirements of electrolysis result in a roundtrip efficiency of approximately 42% for fuel cells and just 17% for hydrogen powered combustion engines.
Although it is possible to compress or liquefy hydrogen and transport it through pipelines or by rail, its properties make this both a challenge and a risk. Hydrogen is the lightest element, escaping even air-tight vessels, and can cause embrittlement in unprotected metals including steel, aluminum, and titanium. This means that repurposing any existing infrastructure, such as natural gas pipelines, would require significant retrofitting.
The storage and transportation of compressed or liquefied hydrogen, like natural gas, also poses a significant risk of combustion when exposed to oxygen. This could pose a major public safety risk. Storing or transporting compressed or liquefied hydrogen will require stringent oversight, possibly exceeding the precautions used in the natural gas industry.
Ammonia to the Rescue?
Ammonia (NH3) contains 17.8% hydrogen by weight. Today, about 70% of ammonia is used for the synthesis of agricultural fertilizers. The remaining 30% is used in a wide array of industrial chemicals including many plastics and explosives. Very little ammonia is used today as an energy vector, and nearly all ammonia is produced from fossil fuels.
A process to store renewable hydrogen in ammonia could neutralize many of the storage challenges of hydrogen. Hydrogen can be stored in ammonia through the Haber-Bosch process, which combines hydrogen gas with nitrogen gas to make ammonia. Hydrogen can be then extracted when and where it is needed by heating ammonia to high temperatures.
Despite enthusiasm for ammonia as an energy vector, there has been limited analysis of the energy requirements and situational suitability of this additional phase in the hydrogen storage cycle. Because carbon-neutral production of hydrogen is already so energy intensive, any additional energy needed for storage, extraction, and transportation may jeopardize the scalability and sustainability of this proposed storage solution.
The Energy Demands of Storing Hydrogen and Ammonia
Synthesis and conversion of hydrogen are only the beginning and end of a longer and more energy-intensive process for successfully using hydrogen as a store of renewable energy. To be efficiently stored and transported (by ship, train, or truck) in its pure form, hydrogen needs to be liquefied or compressed.
Liquefying hydrogen requires cooling below -253°C, the energetic cost of which amounts to ~44.7% of the energy contained in the gas phase (Dias et al. 2020). Although cryogenic storage of hydrogen uses thick vessels that meet stringent sealing and insulation standards, additional energy losses occur due to evaporation (or boil-off) at a rate of about 0.520% of the total volume per day (Al-Breiki and Bicer 2020).
In practice, boil-off losses can be up to 5 vol%/day when little attention is paid to using and maintaining proper insulation (Langeraar 2019). The remaining volume Vr of liquefied hydrogen after d days of storage can be determined by the following expression where Vo is the initial volume of liquefied hydrogen:
Vr= V0 x (1 – 0.0052)d
Per this expression, 1,000 cubic meters (m3) of liquefied hydrogen stored for 100 days would be reduced to 594 m3 solely due to boil-off losses. Boil-off losses, combined with the energy used to liquefy the hydrogen in the first place, results in the short-term (7 days) storage efficiency of 53%, and a storage efficiency of just 21% in seasonal storage applications (182 days), as shown in Figure 1.
Technologies are available to effectively eliminate boil-off losses and can be economically sensible to implement if the cost of operating and maintaining them (such as the cost of electricity to power cryocoolers and the cost of manufacturing multi-layered insulating vessels) is lower than the cost of hydrogen losses that they prevent (Salerno et al. 2002, Notardonato et al. 2017).
To avoid the high energy cost of liquefaction, hydrogen can also be stored and transported at pressures ranging from 350 to 700 bar. At these pressures, adequately sealed vessels can effectively eliminate any leakage.
Though storing hydrogen as a compressed gas is relatively energy efficient (91%) in both short-term and seasonal storage applications, it sacrifices some of the volume savings that high-density liquefied hydrogen enables. Depending on application, this may pose a significant additional logistical challenge.
Ammonia, on the other hand, can be liquefied by either cooling it below -33°C (at atmospheric pressure) or pressurizing it above 7.5 bar (at 20°C)—significantly more achievable conditions than those required for hydrogen. This process can be close to 99% efficient.
Liquefied ammonia also benefits from having an energy density of 3.83 MWh/m3 (Bartels 2008) compared to 2.64 MWh/m3 for liquid hydrogen (Rohland et al. 1992) meaning that liquefied ammonia maintains a higher volumetric energy density than liquefied hydrogen in far less demanding storage conditions.
Ammonia also benefits from a lower boil-off rate (~0.025 vol%/day) (Al-Breiki and Bicer 2020), which contributes to its superior retention of energy potential during long-duration storage and long-distance transportation. Conversely, ammonia storage requires an additional process to extract the hydrogen before use, leading to a small but meaningful decrease in the net energy yield for every ton of hydrogen produced.
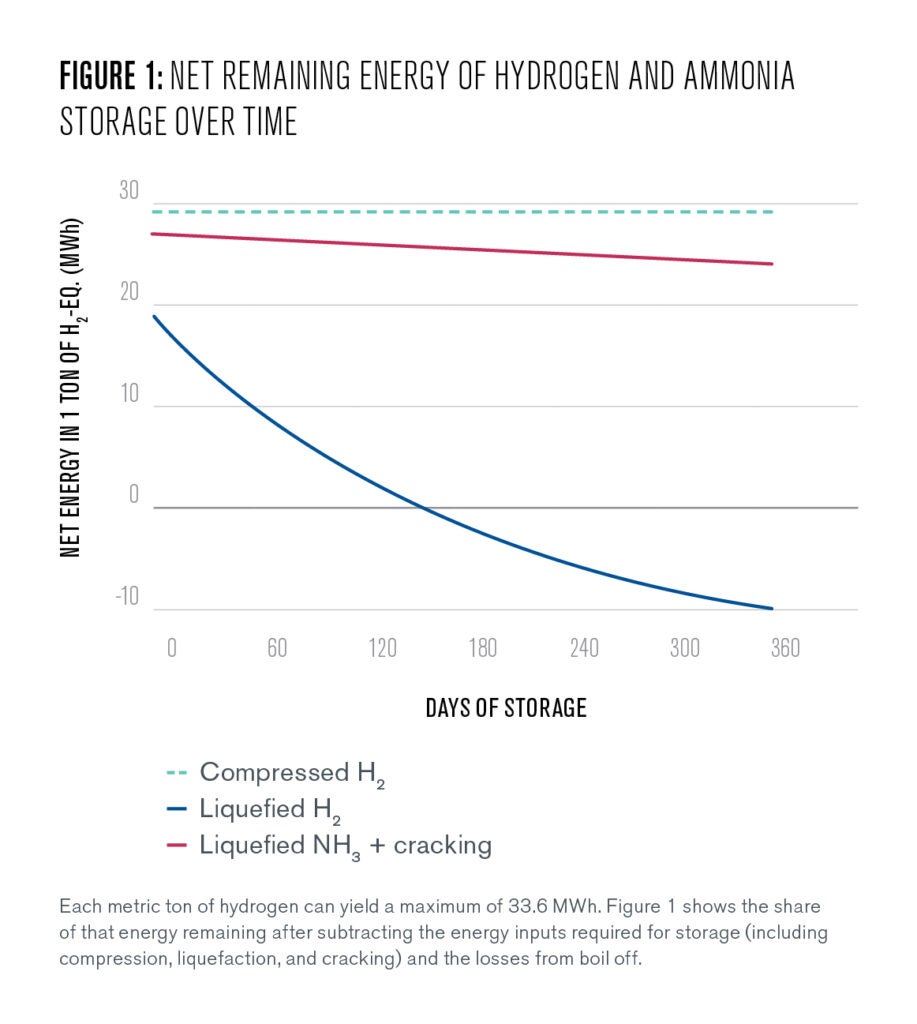
The Energy Demands of Synthesis and Cracking
Clearly, ammonia offers significant advantages in storage and transportation over hydrogen. However, before ammonia can be deemed a viable energy vector, the steps to store and extract hydrogen must be considered.
Synthesis of ammonia is achieved by combining nitrogen gas and hydrogen in the reaction N2 + 3H2 🡪 2NH3. This reaction is realized on an industrial scale through the Haber-Bosch process, which requires demanding reaction temperatures and pressures that necessitate a substantial energy input.
While the theoretical minimum energy required for this process is 6.17 MWh/t-NH3 (34.9 MWh/t-H2), the current best available technology (in terms of efficiency) requires > 7.61 MWh/t-NH3 (43.0 MWh/t-H2) (Smith et al. 2020).
Proposed solutions for renewable hydrogen storage in ammonia are based on variations of the Haber-Bosch process. One possibility is to use hydrogen obtained through electrolysis instead of SMR. The theoretical minimum for such a process is 5.92 MWh/t-NH3 (33.5 MWh/t-H2) (Smith et al. 2020). However, current best available technologies have efficiencies closer to 10–12 MWh/t-NH3 (56.7–68 MWh/t-H2) including the energy required for electrolysis (Giddey et al. 2017).
Extraction of hydrogen from ammonia can be achieved through the ammonia cracking process, 2NH3 🡪 N2 + 3H2. This is also an energy intensive process, typically requiring temperatures exceeding 900oC (Giddey et al. 2017). The high temperatures are required to give high yields of hydrogen.
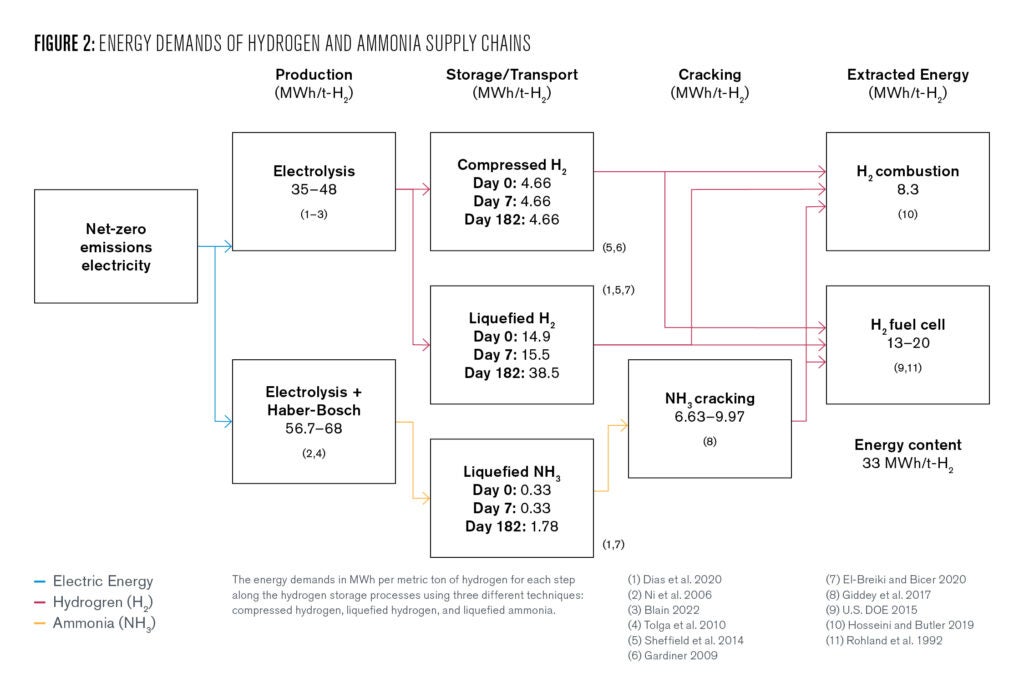
Lower temperatures afford larger concentrations of unreacted ammonia and make the utilization of the product hydrogen challenging due to the high purity demands of fuel cells. The theoretical minimum required for the cracking process is around 0.88 MWh/t-NH3 (5.0 MWh/t-H2 released) (Thomas and Parks 2006), though currently available technologies require 1.17-1.76 MWh/t-NH3 (6.63 – 9.97 MWh/t-H2) (Salmon and Bañares-Alcántara 2021).
Comparing Energy Efficiencies
Generally, compression of hydrogen, rather than liquefaction of ammonia or hydrogen, is the more energy efficient method of storing hydrogen, if space and transportation are not a limiting factors. This is attributable to the boil-off rates associated with hydrogen liquefaction and the energy costs of ammonia synthesis and cracking. Compressed hydrogen still requires energy for the initial compression process, but once it is fully sealed and stable within appropriately-rated canisters or pipelines, it has effectively zero losses.
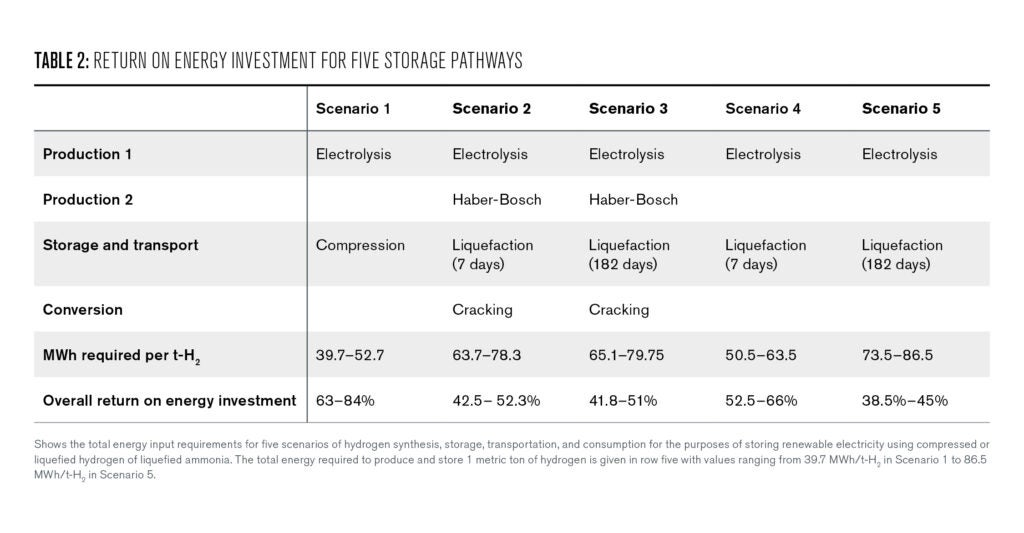
Both ammonia and hydrogen liquefaction experience constant boil-off, reducing the roundtrip efficiency of these pathways over time. However, while the boil-off rate of ammonia only reduces the stored energy by a small fraction over a six-month storage period, the overall quantity of liquefied hydrogen falls by close to 60% over that same period.
Furthermore, ammonia can be liquefied using only a small fraction of the stored energy, while liquefying hydrogen requires almost 50% of the stored energy. This comparative advantage of ammonia is somewhat offset, however, by the synthesis and cracking of ammonia. Ultimately, the roundtrip energy efficiency of liquefied ammonia and hydrogen for 182 days is comparable, with range overlaps between 41.8–45%
If a liquid fuel is required, the choice between liquefied hydrogen and ammonia will depend on a number of factors including the efficiency of electrolysis, ammonia synthesis, and ammonia cracking, the expected duration of storage, and the available storage and transportation infrastructure.
If we assume a 40 MWh/t-H2 energy cost of electrolysis, a 60 MWh/t-H2 cost of renewable ammonia synthesis, and 8 kWh/t- H2 for ammonia cracking, we can use the boil-off rates of both fuels to calculate a break-even point of 11 days. Before this point, liquefied hydrogen is more energy efficient than ammonia. After this point, the energy demands for ammonia synthesis and cracking are overtaken by the combined energy demands of electrolysis and liquefied hydrogen storage.
However, slight variations in the assumed efficiencies of reactions or changes in the boil-off rate for hydrogen or ammonia could significantly impact the time frame for this break-even point. The efficiency ranges in Table 2 demonstrate the difficulty in precisely calculating the return on energy invested for any of the five storage scenarios.
On the other hand, using ammonia directly as an energy source through combustion produces toxic NOx gasses, necessitating NOx scrubbers at any point of direct combustion. Current studies on ammonia combustion have widely explored using ammonia fuel blends with hydrogen or traditional fossil fuels in combustion engines.
In general, lower purities of ammonia creates more CO2 and NOx emissions, and distributed scrubbing would be difficult to regulate (Erdemir 2020). It is worth mentioning that while energy generation through combustion of 100% ammonia eliminates the possibility of CO2 emissions, it may still produce NOx due to the partial oxidation of ammonia or the product nitrogen gas.
Tapping into Pipeline Infrastructure
Independent of the roundtrip efficiency of each fuel, one of the most commonly stated advantages of ammonia over compressed hydrogen or liquefied hydrogen is that it could benefit from the extensive existing ammonia pipeline infrastructure used primarily by the agriculture sector.
The United States, for example, has a network of more than 5,000 kilometers of pipeline in operation today. Recently, this pipeline network shrank with the decommissioning of the 1,800-km Magellan pipeline, which connected the Southern Plains and Western Corn Belt with production facilities in Texas and Oklahoma; however, it still exceeds existing hydrogen transport infrastructure (~2,500 km in the United States) (Bouwkamp et al. 2017).
For comparison’s sake, the U.S. has 490,000 kilometers of high-pressure natural gas transmission pipelines and over 3 million kilometers of lower-pressure natural gas distribution pipelines for last-mile delivery to end users (Hydrogen Council and McKinsey 2021). Neither the existing hydrogen nor the existing ammonia infrastructure comes anywhere close to meeting the demands of a heavily hydrogen-dependent energy system, and therefore does not offer either fuel a significant leg up.
Globally, demand for ammonia is equivalent to 176 million metric tons per year. If hydrogen were to replace the energy demands of just 50% of present-day natural gas, it would require at least 3.49 billion metric tons of ammonia per year. This represents a 20-fold increase in global ammonia production and a similar increase in available transportation and storage infrastructure.
The story is the same for hydrogen. Today, global hydrogen production is approximately 74 million metric tons. To meet 50% of the energy demand currently met by natural gas would require at least 617 million metric tons per year—an increase of more than 800%.
Arguably, the true infrastructure advantage lies in how these two energy vectors can make use of existing natural gas infrastructure. Fuel pipelines are notoriously difficult to complete. They are expensive, require collaboration across multiple jurisdictions, and often meet fierce public resistance and legal roadblocks.
The repurposing of existing natural gas pipelines to transport carbon-neutral alternative fuels offers an invaluable opportunity to bypass many of these new infrastructure challenges. The energy transition will require enormous infrastructure investments, but any opportunity to utilize existing infrastructure can save time and cut costs.
Repurposing natural gas pipelines to transport hydrogen would require extensive modifications, which include replacing components such as compressors, valves, pressure regulators, and sealing membranes to conform with the flow properties of hydrogen. Aging pipelines that are at or near the end of their lifetimes would need to be replaced.
Additionally, as hydrogen is known to cause embrittlement and premature cracking in steel, it might be more prudent to use novel embrittlement-resistant grades of steel or fiber-reinforced polymers in any new pipeline construction (Bouwkamp et al. 2017). Existing pipelines that are deemed safe to carry hydrogen could benefit from a polymer coating on their inner walls to enhance their resistance to embrittlement and, thus, their operating lifetime.
In financial terms, retrofitting existing land transmission pipelines to carry hydrogen could cost between $0.6 and $1.2 million per kilometer, while the cost of constructing new pipelines could be between $2.2 and $4.5 million per kilometer (Hydrogen Council and McKinsey 2021).
Retrofitting existing natural gas infrastructure for ammonia may be significantly more involved, since the characteristics of existing ammonia pipelines are quite distinct from natural gas pipelines. Whereas natural gas transmission pipelines are typically pressurized to 500–1,200 psi, ammonia pipelines typically operate at just 250 psi. At this pressure, ammonia is a relatively heavy liquid.
This means that if natural gas pipelines were to be repurposed for ammonia transport, they would either need to be adapted to operate at much lower pressures or under a much higher weight burden. On the other hand, liquid ammonia is non-corrosive and does not exhibit the same embrittlement properties as hydrogen, meaning that materials restrictions are not as stringent.
Policy Recommendations
As we transition away from fossil fuels and toward inherently variable generation technologies, it is essential that we develop affordable and sustainable solutions for moving and storing energy. Batteries and the electricity grid will accommodate and balance much of this load, but there are likely to be some energy and storage needs for which electrochemical batteries and transmission lines will be poorly suited. Stable liquid or gaseous renewable fuel may still be needed for long-term seasonal storage, high heat processes, and poorly integrated demand centers.
Hydrogen is, in many respects, an ideal vector for energy transfer. It can be produced from water and electricity and has a very high energy potential by weight. However, as this analysis makes clear, it is a difficult and costly fuel to store. Our findings indicate that compressing hydrogen is the most energy efficient method of storing and moving it, but this requires extensive pipeline retrofits and bulky storage containers.
Liquefied hydrogen improves on storage density but is even more challenging to store and transport without significant boil-off losses. Ammonia is a relatively stable and easy to transport vector for hydrogen, but the energy costs of synthesis and cracking are considerable and, over short storage durations, this method offers lower return on energy investment than the compressed and liquefied hydrogen pathways.
Since compressed hydrogen shares many similarities with natural gas and can be blended into existing natural gas supplies, this analysis concludes that developing new infrastructure and retrofitting existing infrastructure for the storage and transportation of compressed hydrogen is the strongest path forward for realizing the full potential of hydrogen as a store of renewable energy.
Recent analyses suggest that blending hydrogen into natural gas may not be an effective long-term decarbonization solution. In a first-of-its-kind demonstration in New York, a blend with 44 vol% hydrogen only reduced the carbon dioxide emissions of natural gas combustion by 20 % (EPRI, NYPA, and GE 2022). Nevertheless, retrofitting pipelines to allow for blending and eventually exclusive transportation of hydrogen to demand centers and distributed fuel cells could repurpose existing infrastructure and reduce the burden placed on new electricity transmission infrastructure in the long run (Topolski et al. 2022).
Although ammonia offers a more energy-efficient method than liquefied hydrogen for storing hydrogen on the scale of weeks or months, this analysis suggests that from both an energy efficiency standpoint and an infrastructure standpoint, compressed hydrogen offers the best hydrogen storage solution in most situations.
Oscar Serpell
Deputy DirectorOscar Serpell oversees all student programming, alumni engagement, faculty and student grants, and visiting scholars. He is also a researcher, writer, and policy analyst working on research initiatives with students and Center partners.
Zakaria Hsain
Postdoctoral Researcher, University of PennsylvaniaZakaria H’sain is a postdoctoral researcher in the Pikul Group at the University of Pennsylvania. He holds a Ph.D. in mechanical engineering and applied mechanics from Penn and is a former Kleinman Center research assistant.
Wan-Yi “Amy” Chu
Assistant Professor, St. Mary’s College of CaliforniaAmy” Chu is an Assistant Professor of Chemistry at St. Mary’s College of California and a former postdoctoral researcher in the Goldberg Group located in the Department of Chemistry at the Univrsity of Pennsylvania.
Walter Johnsen
Student Advisory Council MemberWalter Johnsen is a Ph.D. candidate in the department of chemistry and he was the 2022 Kleinman Philadelphia Energy Authority Fellow. He is also a member of the Kleinman Center’s Student Advisory Council.
Al-Breiki, Mohammed, and Yusuf Bicer. 2020. “Comparative Cost Assessment of Sustainable Energy Carriers Produced from Natural Gas Accounting for Boil-Off Gas and Social Cost of Carbon.” Energy Reports 6: 1897–1909. https://doi.org/10.1016/j.egyr.2020.07.013.
Bartels, J R. 2008. “A Feasibility Study of Implementing an Ammonia Economy.” Iowa State University. https://lib.dr.iastate.edu/cgi/viewcontent.cgi?article=2119&context=etd.
Black & Veatch. 2020. “Hybrid LNG & Ammonia Infrastructure: Key to a Green Economy.” https://doi.org/10.31826/9781463236762-toc.
Bouwkamp, Nico, Al Burgunder, Dan Casey, Amgad Elgowainy, Leah Fisher, Jim Merritt, Eric Miller, et al. 2017. “Hydrogen Delivery Technical Team Roadmap.” https://www.energy.gov/sites/prod/files/2017/08/f36/hdtt_roadmap_July2017.pdf.
Dias, Véronique, Maxime Pochet, Francesco Contino, and Hervé Jeanmart. 2020. “Energy and Economic Costs of Chemical Storage.” Frontiers in Mechanical Engineering 6. https://doi.org/10.3389/fmech.2020.00021
EPRI, NYPA, and GE. 2022. “Hydrogen Cofiring Demonstration At New York Power Authority’s Brentwood Site: GE LM6000 Gas Turbine.” https://restservice.epri.com/publicdownload/000000003002025166/0/Product.
Erdemir, Dogan, Ibrahim Dincer. 2020. “A Perspective on the Use of Ammonia as a Clean Fuel: Challenges and Solutions.” International Journal of Energy Research 45 (4). https://doi.org/10.1002/er.6232
Folga, S.M. 2007. “Natural Gas Pipeline Technology Overview.”
Giddey, S., Badwal, S. P. S., Munnings, C., and Dolan, M. 2017. “Ammonia as a Renewable Energy Transportation Media.” ACS Sustainable Chemistry & Engineering 5: 10231 – 10239
Hernandez, Drake D., and Emre Gençer. 2021. “Laying the Regulatory Groundwork for Hydrogen in the United States.” Utility Dive. https://www.utilitydive.com/news/laying-the-regulatory-groundwork-for-hydrogen-in-the-united-states/601408/.
Hydrogen Council, and McKinsey & Company. 2021. “Hydrogen Insights.” https://hydrogencouncil.com/wp-content/uploads/2021/02/Hydrogen-Insights-2021.pdf.
Langeraar, Jan Willem, Marcel Keezer, and Ruud Bakker. 2019. “Workshop: Challenges for the Production and Application of Liquefied Hydrogen.” https://prod5.assets-cdn.io/event/3757/assets/8431103583-8e79cc08e1.pdf.
Loginow, A.W., and E.H. Phelps. 1962. “Stress-Corrosion Cracking of Steels in Agricultural Ammonia.” Corrosion 18.
Mauler, Lukas, Fabian Duffner, Wolfgang G. Zeier, and Jens Leker. 2021. “Battery Cost Forecasting: A Review of Methods and Results with an Outlook to 2050.” Energy & Environmental Science 14: 4712-4729
Notardonato, W. U., A. M. Swanger, J. E. Fesmire, K. M. Jumper, W. L. Johnson, and T. M. Tomsik. 2017. “Zero Boil-Off Methods for Large-Scale Liquid Hydrogen Tanks Using Integrated Refrigeration and Storage.” IOP Conference Series: Materials Science and Engineering 278 (1). https://doi.org/10.1088/1757-899X/278/1/012012.
Rohland, B., J. Nitsch, and H. Wendt. 1992. “Hydrogen and Fuel Cells: The Clean Energy System.” Journal of Power Sources 37 (1–2): 271–77. https://doi.org/10.1016/0378-7753(92)80084-O.
The Royal Society. 2020. “Ammonia: Zero-Carbon Fertilizer, Fuel and Energy Store.” https://royalsociety.org/-/media/policy/projects/green-ammonia/green-ammonia-policy-briefing.pdf.
Salerno, L. J., J. Gaby, R. Johnson, P. Kittel, and E. D. Marquardt. 2002. “Terrestrial Applications of Zero-Boil-Off Cryogen Storage.” In Cryocoolers 11, edited by R.G. Ross Jr., 809–16. https://doi.org/10.1007/0-306-47112-4_98.
Salmon, Nicholas, and René Bañares-Alcántara. 2021. “Green Ammonia as a Spatial Energy Vector: A Review.” Sustainable Energy & Fuels 5: 2814 – 2839
Smith, Collin, Alfred K. Hill, and Laura Torrente-Murciano. 2020. “Current and Future Role of Haber-Bosch Ammonia in a Carbon-Free Energy Landscape.” Energy & Environmental Science 13: 331-344
Topolski, Kevin, Evan P Reznicek, Burcin Cakir Erdener, Chris W San Marchi, Joseph A Ronevich, Lisa Fring, Kevin Simmons, Omar Jose Guerra Fernandez, Bri-Mathias Hodge, and Mark Chung. 2022. “Hydrogen Blending into Natural Gas Pipeline Infrastructure: Review of the State of Technology.” Golden, CO. www.nrel.gov/docs/fy23osti/81704.pdf.
U.S. Department of Energy. 2006. Potential Roles of Ammonia in a Hydrogen Economy: A Study of Issues Related to the Use of Ammonia for On-Board Vehicular Hydrogen Storage. by George Thomas and George Parks, https://www.energy.gov/eere/fuelcells/downloads/potential-roles-ammonia-hydrogen-economy